

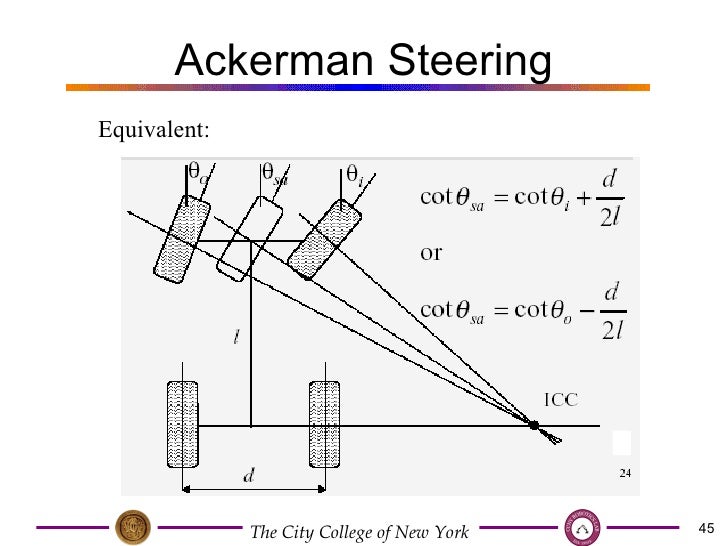
The Linear Quadratic Regulator and the Deep Deterministic Policy Gradient (DDPG) are compared for robust control when the trailer is changed. Reinforcement learning, with neural networks as their function approximators, can allow for generalized control from its learned experience that is characterized by a scalar reward value. Finding alternative robust controllers when the trailer model is changed was the motivation of this research. However, real-world applications cannot expect to have an updated model for each new trailer. The closed form calculation of the gains for the Linear Quadratic Regulator (LQR) rely heavily on having an accurate model of the plant. The combination vehicles can be varied in wheelbase, hitch length, weight distributions, and tire cornering stiffness. Starting from random locations and orientations, paths are generated to loading docks with arbitrary pose using Dubins Curves. Two controller performances are assessed for generalization in the path following task of autonomously backing up a tractor-trailer. Basic economic calculations estimated the cost to operate the Flex-Ro machine for field phenotyping use at approximately $5.50/ha. The late season phenotyping data showed statistical differences between the fully irrigated versus deficit plots. The Flex-Ro was able to statistically distinguish between soybean variety emergence and maturity differences. Positive correlations between the Spidercam and Flex-Ro phenotyping data were established. The system was verified in soybean research plots at the University of Nebraska-Lincoln (UNL) Spidercam phenotyping facility. A suite of phenotyping sensors was installed onto the Flex-Ro to cover large field areas.
Ackermann steering geometry calculator manual#
The methods used to collect phenotyping data include drones, satellites, manual measurement, and ground rovers.
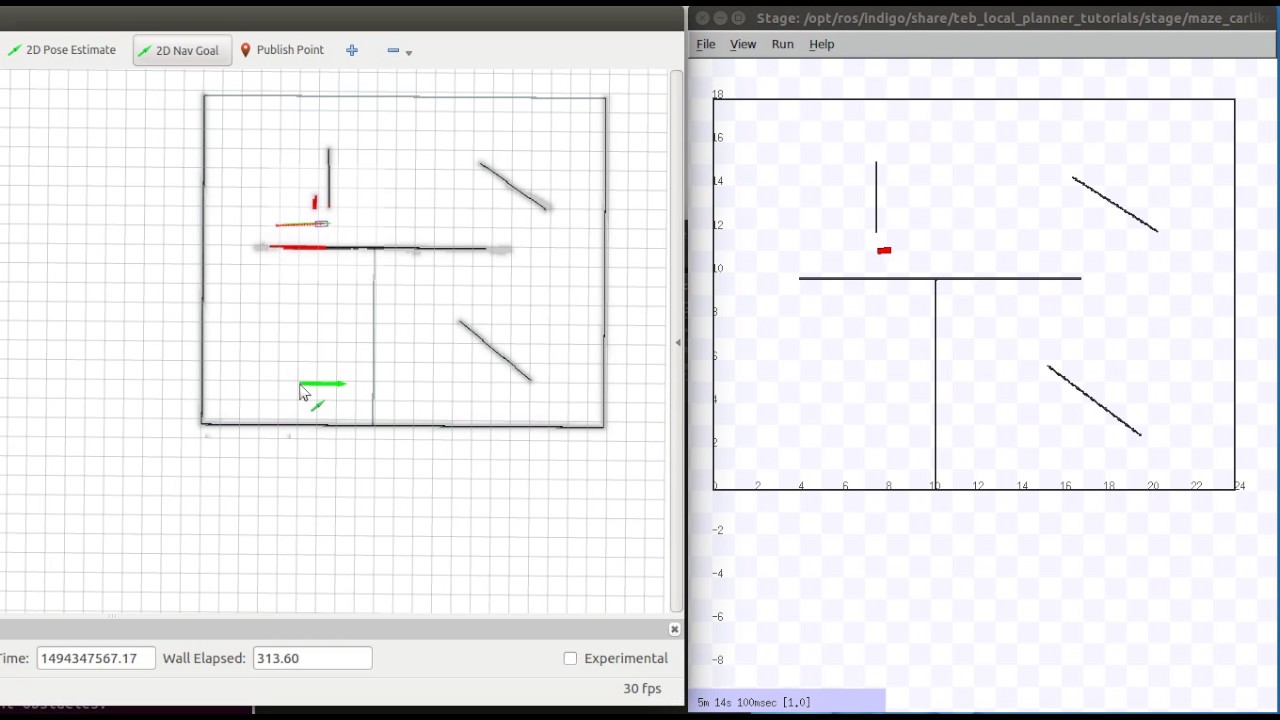
High-throughput plant phenotyping is a continuously developing and evolving field of plant science. Waypoint guidance was implemented and demonstrated such that Flex-Ro could be programmed to follow complex paths and curves. The guidance system tracked within 4 cm of the guidance line 95% of the time at a travel speed of 4 kph. Autonomous field coverage was developed using global positioning system (GPS) guidance. Operators use the remote-control device to maneuver the machine in uncontrolled environments. The machine control architecture was developed for safe operation with redundant emergency stops and checks. This work presents the design and implementation of the control system for the Flex-Ro machine. The Flex-Ro (Flexible structured Robotic platform) was developed for use in large area fields as a multipurpose tool to perform monotonous agricultural tasks. However, the use of autonomous robots in commercial agricultural production is still limited. The use of robotics has been adopted in several industries to supplement labor, and accurately perform repetitious tasks. Optimization of crop production per unit of land requires scientists across disciplines to collaborate and investigate new areas of science and tools for data collection. In order to satisfy the fundamental equation for correct steering, the links AK and KL are suitably proportioned and angle alpha is suitably selected.Research in agriculture is critical to developing techniques to meet the world’s demand for food, fuel, fiber, and feed. When the vehicle is running straight, the crosslink KL is parallel to AB, the short arm AK and BL both make angle alpha to the horizontal axis of chassis. The Ackermann steering gear mechanism consists of a cross link KL connected to the short axles AC and BD of the two front wheels through the short arms AK and BL, forming bell crank levers CAK and DBL respectively. This system is called ackermann steering. The track arms are made inclined so that if the axles are extended they will meet on the longitudinal axis of the car near rear axle. It is not mathematically accurate except in three positions. The range of b / l is 0.4 to 0.5 hence angle alpha lies between 11.3 and 14.1 0.Īckermann Steering Gear has only turning pair. Where b=AB=distance between the pivots of front axles. The correct steering depends upon a suitab1e selection of cross-arm angle alpha, and is given by The short arms AK and BL are inclined an angle 90+alpha to their stub axles AC and BD. The slide blocks are pivoted on these pins and move with the turning of bell crank levers as the steering wheel is when the vehicle is running straight, the gear said to in its mid-position. The cross link KL slides in slides in the bearing and carries pins at its end K and L. The Davis gear mechanism consists of a cross link KL sliding parallel to another link AB and is connected to the stub axles of the two front wheels by means of two similar bell crank levers ACK and DBK pivoted at A and B respectively.
